Total Weld ReMan
Our Total Weld ReManufacturing (ReMan) service provides complete reconditioning for the outer diameter of large hydraulic rods and industrial rollers. Our welding professionals ensure precise and durable welds that restore the structural integrity of each component.
Utilizing state-of-the-art automated equipment and advanced techniques, we meticulously repair and strengthen equipment to withstand heavy loads and harsh operating conditions. Whether the component has suffered from scarring, stroke wear, or other damage, our submerged arc welding process provides reliable and long-lasting results.
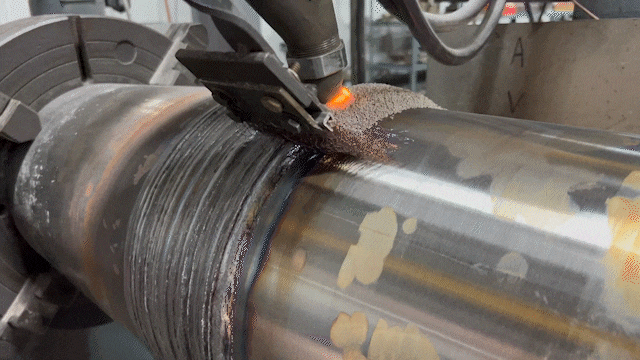
Typical candidates:
- Strut cylinder rods from haul trucks
- Industrial press rods
- Long wall cylinder rods
The most cost-effective solution on the market:
- Our submerged arc welding (Total Reweld) repair costs only 10-20% of what OEM replacement components cost.
- Once the rod has been repaired and plated, it can usually be repaired with our standard re-chrome process up to 3 times before needing another re-weld. This makes it 50-60% cheaper than HVOF coatings over the life of the rod.
How Our Total Weld ReManufacturing Process Works
Prep Process
Our initial inspections include crack checks and hardness tests. After initial inspection, we use heavy-duty lathes and tooling to remove the outer layer, including any damage and scarring. We complete the preparation for weld by performing a thorough preheat of the component. The preheat helps prepare the base metal for weld and prevent cracking after weld.
Submerged Arc Welding
Our experienced welding team uses an automated submerged arc welding system to perform a comprehensive re-weld of the component using various wire and flux combinations unique to each component. Special temperature control measures ensure optimal bonding and structural integrity of the base metal.
Post-Weld Process
After weld, the component is slowly cooled at a specified rate. This relieves stress and avoids potential cracking issues. We then remove the extra weld layer and bring the component back to size, preparing it to enter the chrome plating process. A final crack check ensures no cracks prior to chrome plating.
Final Quality Inspections
We understand the importance of quality control in heavy-duty components. Our experts perform a final rockwell test, chrome thickness test, and visual inspection of all subwelded components. All quality inspection results are logged, along with photographs, for quality control.
Our Services
Expansive in-house capabilities allow us to keep all facets of the chrome plating and repair process under our control.