Chrome Plating & Repair Process
Our process is completed in 4 phases, each designed to ensure that the finished component is at size specification
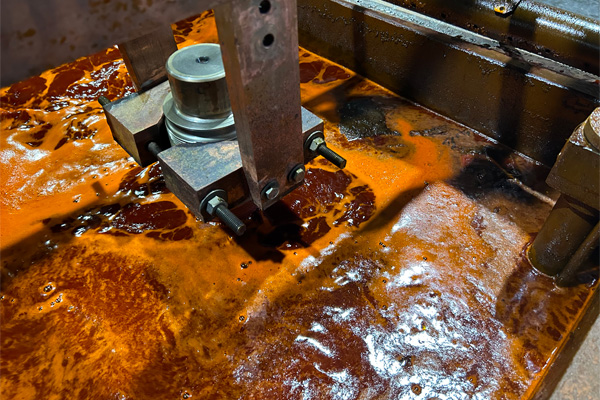
Step 1: Remove Existing External Layer
Our chrome stripping baths use caustic chemical to remove chrome and other debris from the part. Once the external layers are removed, the part is thoroughly washed.
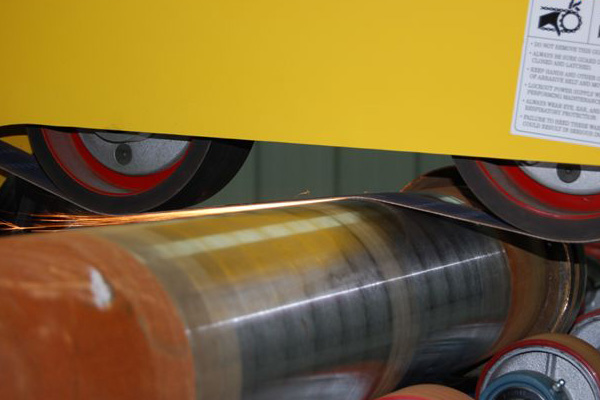
Step 2: Preparation
Our grinding machinists review the part specifications, requirements, and customer needs. We use abrasive belts and cylindrical grinding equipment to even out any variances in the part and bring it to slightly below its diameter specification.
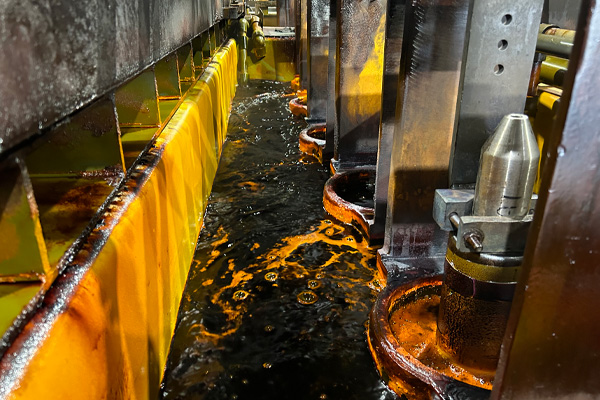
Step 3: Hard chrome plating
Our highly experienced plating team calculates the required current density to plate the part back to its size specification using a hard chrome layer. The part is loaded into a cylindrical anode and high levels of DC current are induced. An electrochemical reaction bonds the chromium to the base metal. After plating, the part undergoes another thorough wash and degrease.
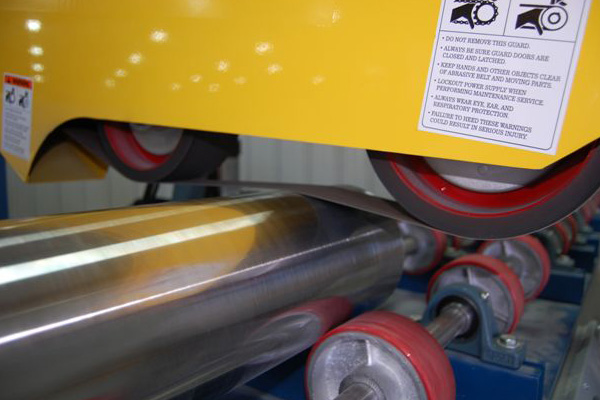
Step 4: Polishing
Finally, our polishing machinists remove any imperfections and take final grinding passes to ensure that the part is not only on size, but has a near-mirror finish! We wrap our parts in corrugated cardboard when complete in order to protect the chrome layer from incidental contact during delivery.